Playback speed in this video was increased while the gripper accessed another pallet from the machine’s storage rack.
Challenge Machine takes advantage of a laser probe installed on the side of its new five-axis machine’s swiveling B-axis casting for tool presetting and, during an unattended machining cycle, to check for tool breakage and track tool wear (for some applications).
Blaine, Minnesota’sChallenge Machinespecializes in machining small, complex parts — some exceedingly small. It does this using a range of equipment, including B-axis Swiss-type lathes, VMCs with trunnion tables that provide fourth- and, in some cases, fifth-axis rotation, and high-speed, true five-axis machining centers.
Featured Content
尽管该商店已经能够使用其酒吧喂养的瑞士人类型实现长时间的无人看管的加工,但直到最近其所有铣削设备都需要手动零件装载。但是,其最新的五轴机器具有集成的劳动托盘更换器和高容量的自动工具汇用(ATC),使其能够在白天无人看管和晚上的灯光运行。此外,CNC功能与触摸式例程相结合,简化了编程,因为操作是基于创建一个工作坐标系的一个运动点创建的。
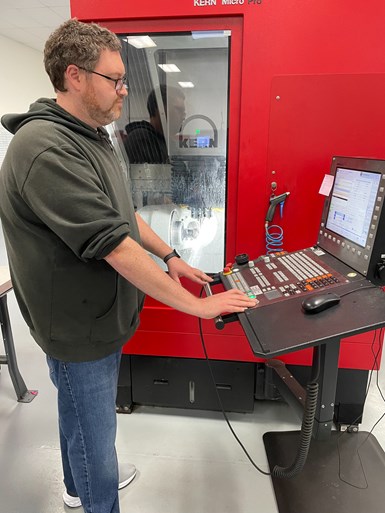
机械师布兰登·吉尔(Brandon Gill)是Micro Pro的主要程序员,设置人员和操作员。他赞赏诸如使用Micro Pro的Heidenhain TNC 640 CNC和探测常规的功能,例如基于一个运动点/工作坐标系进行编程操作的功能,而不是使用G54或G55 G代码外部进行编程。
The automated five-axis machine is a Micro Pro from Germany’s Kern Microtechnik (known in the United States asKern Precision,位于伊利诺伊州艾迪生)。挑战机器总经理亚伦·施雷伯(Aaron Schreiber)表示,这家商店一直在考虑这个复杂的机器平台已有15年了,他承认一家人代表了不小的投资。但是,这家商店决定在2019年底拉动扳机,因为它经历了越来越多的医疗零件的准确性,可重复性和表面饰面问题,ISO 13485认证的商店正在其一些五轴Trunnion机器上运行。另外,他指出,整个新机器中的冷却通道诸如减轻热增长的特征,还促进了通常具有较长周期时间的复杂零件的可靠加工。除其他机器功能外,这还使商店有信心将其设置为自行运行数天甚至数周。
Let It Run
Jim Betland started Challenge Machine in his basement in 1999. Early on, a large portion of the business was devoted to micromachining parts for the semiconductor industry. The shop, recently purchased by Assurance Manufacturing in Minneapolis, still focuses on the small stuff. (I’m talking in terms of part size and minding important micromachining details.) Schreiber says sales are up 15% this year as the shop increases its focus on the medical market while also targeting aerospace work.
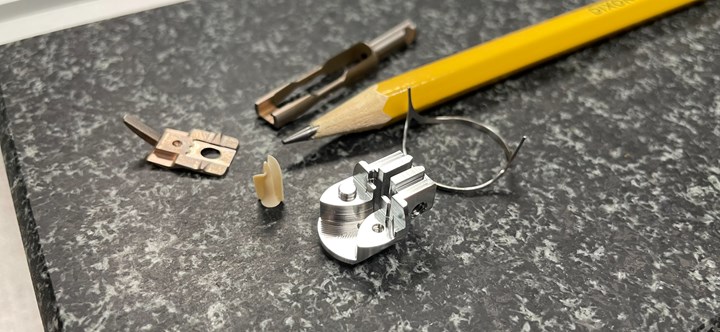
The shop has machined a range of parts from various materials on the Micro Pro. In a typical month, it runs 10 to 15 different part numbers across the machine, many having cycle times upward of 3 hours.
According to Kern, the Micro Pro — which features hydrostatic guides, linear drives and a single-casting base made from ultra-high-performance concrete (UHPC) — achieves better than 2 microns positioning accuracy and better than 1 micron repeatability. It was designed with small-parts machining in mind, offering XYZ travels of 350 by 220 by 250 mm, while its swiveling B axis rotates 220 degrees. Schreiber notes that its small footprint of 43 square feet is appreciated given that floor space is currently at a premium in the shop’s 16,000-square-foot, environmentally controlled facility. (He says this is one reason the shop is likely to move to a different location in the coming years.)
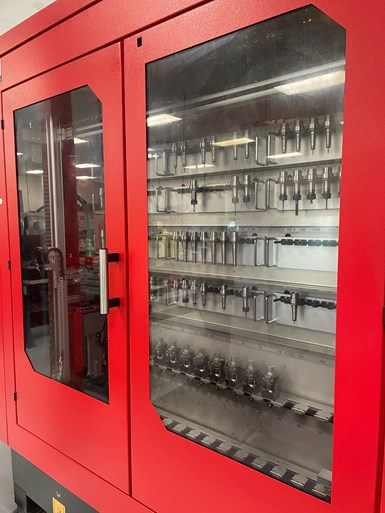
Cutting tools and workholding pallets are stored on the side of the machine. This machine can accommodate 30 workholding pallets and 109 tools. The smallest tool the shop has used on the Micro Pro (which has a 43,000-rpm HSK 40 spindle) is 0.003 inch in diameter.
Challenge Machine’s Micro Pro uses anErowazero point workholding system with power chuck that provides repeating positioning accuracy of less than 0.0001 inch. The machine can store 30 pallets and 109 toolholders in its enclosed, multilevel racks along one of its sides. The integral workpiece changer automatically delivers pallets with raw material (commonly round stock held in collets in Challenge Machine’s case) to the chuck, and removes and stores pallets once parts are completed.
工件和工具存储容量提供了shop versatility in the types of jobs it runs across the machine. For example, redundant tooling can be loaded into the machine when batch sizes of the same or similar parts are high. (Schreiber says batch sizes for this machine typically tops out at 100 to 300 pieces.) Conversely, various different tools (and pallets with raw material) can also be loaded so it can concurrently run a mix of low-volume jobs.
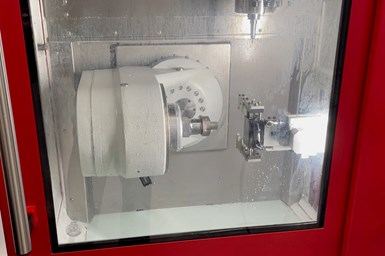
The integral workpiece changer automatically delivers pallets with material (commonly round stock held in collets) to the worktable and removes pallets once parts are completed. An Erowa zero-point workholding system features power chucks that provide repeating positioning accuracy of less than 0.003 mm.
Although batch sizes for this machine are seemingly low (much of the shop’s work is prototypes and low production volumes), part cycle times are often high. It sometimes runs unattended for 3 weeks straight, and 3-hour cycle times for a part are not uncommon. For example, the Micro Pro completes a titanium medical component used for aortic valve repair having walls measuring 0.014-inch-wide from 1.25-inch-diameter barstock in which 97% of the material is removed.
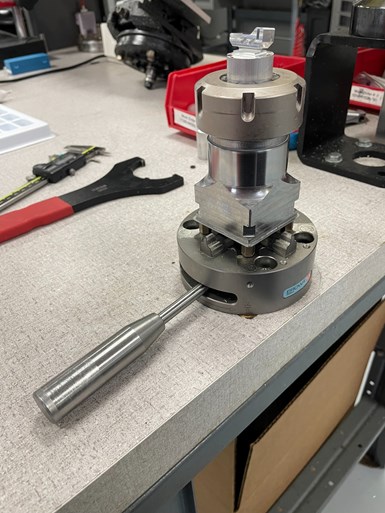
Here, a chuck is used simply for manual unloading of completed parts and loading of new material.
对于诸如此类的应用和血泵的叶轮,需要进行全五轴轮廓。但是,该商店还通过为更多的棱柱形零件执行3 + 2个定位操作而受益,而不是在多台机器上运行或执行多个设置。
To offer further confidence to run the Micro Pro unattended, Challenge Machine takes advantage of theBlum-Novotestlaser probe which is mounted on the side of the machine’s swiveling B-axis casting for tool presetting and, during unattended machining cycles, to check for tool breakage and track tool wear (for some applications).
Read: Swiss Shop’s Choice of Collets Facilitates Backworking
机械师布兰登·吉尔(Brandon Gill)是Micro Pro的主要程序员,设置人员和操作员。他说,这台机器的一个小挑战越来越熟悉HeidenhainTNC 640 CNC(商店的第一个品牌),尽管这只是熟悉CNC的界面以及访问特定功能的问题。他赞赏诸如使用TNC 640 CNC基于一个运动点/工作坐标系编程操作的功能,而不是使用G54或G55 G代码偏移进行编程。商店使用GibbsCAMto develop part programs for this machine as it does with its other milling machines.
In fact, Gill notes that capabilities like these are why the Micro Pro is his preferred machine to program and operate.
相关内容
Selecting A VMC: Things To Consider
A three-, four- or five-axis vertical machining cneter can run the gamut of capability and cost. Assessing your application requirements now and in the future can make for a much wiser machining center purchase.
Get 5-Axis Machining on a 3-Axis VMC
Machine shops want and need to eliminate steps in the manufacturing process. Adding four- or five-axis capability to an existing three-axis VMC is a practical way to achieve five-sided machining using a single setup.
Keeping Watch on Small Parts
从手表零件到异国医学应用,这家商店都融入了微加工的世界。