What A Former Moldmaker Has Learned About AM: Leverage Simplicity and Let It Scale
Appears in Print as:'Linear’s Future is Additive'
The once-again independent Linear AMS is now more focused on additive manufacturing than ever before.

不再需要通过成型制作的自动独立原型零件的示例。
Yet the company will still fill much the same niche. Linear built a reputation manufacturing mold tooling for the automotive industry, including prototype molds aimed at producing just hundreds or thousands of parts for vehicles still in development. This work came to be characterized by low margins and delayed payment terms, leading company CEO John Tenbusch to turn a different way. Today, he offers automotive-industry customers the chance to skip moldmaking for prototypes as he instead 3D prints the parts using Multi Jet Fusion machines fromHP.
Featured Content

John Tenbusch led his business to invest in metal additive manufacturing over a decade ago. Linear remains a user of EOS equipment, which the company now uses solely to create conformal-cooled inserts for moldmakers.
The name "Linear" has been associated with additive manufacturing for years. Indeed, the name has been associated with the brandAdditive Manufacturing(that is, us), because the company then known as Linear Mold & Engineering additively produced the3D aluminum model of our new logo

The Multi Jet Fusion 3D printing is the most scalable part of the business. Production is largely contained within the machines, and an ongoing 3D printing job could commit the capacity of a machine or two.
Tenbusch的规定很好,因为有一段时间,它迫使他专注于金属AM的线性专业,包括保形冷却通道在内的霉菌插件(即,遵循模具表面的形式,非转弯冷却通道,以便更快地零件冷却并减少成型周期时间)。新独立Linear AMS(the letters stand for "Additive Manufacturing Services") coupled this capability with moldmaking in a conventional mold shop, plus injection molding in a facility dedicated to this, plus polymer 3D printing via Multi Jet Fusion — the most recent capability added.
但是从某种意义上说,霉菌制造的构成了线性的添加剂制造。他说,制作3D打印的模具插件意味着向霉菌商店出售,“我们会以竞争对手的身份退缩。”对汽车工具的限制将于2020年1月结束,因此这种阻塞并不是一个严重的挑战。尽管如此,它还是揭示了
Make It Simple
Indeed, what Tenbusch has learned is that additive manufacturingwantssimplicity. “Find the application you know best how to deliver and make it as simple as possible to do it,” he says. On Linear’sEOSmetal additive machines, that meant no more maintaining different choices of material. The machines currently run only MS1 steel, no other choice. It also means no machining whatsoever. Customers get a build plate with the tool still attached. These customers are mold shops, so they know how to square the insert to the dimensions they want.
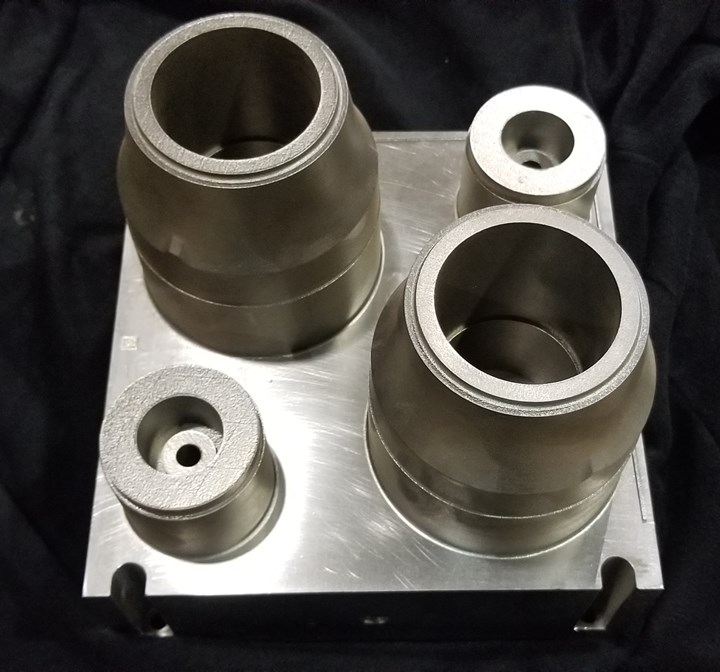
Linear does not do machining anymore, including completing conformally cooled mold inserts such as this one (for a mold related to the appliance industry). Instead, inserts are shipped still attached to the AM build plates. The mold shop receiving the insert cuts it away and fits it into the mold.
In this light, here is how the owner of Linear AMS thinks about his capabilities now, and how he sees the set of capabilities that will help carry the company into the future:
•Metal Additive Manufacturing
Metal AM continues at Linear as a means of making conformal-cooled inserts.
• InjectionMolding
In other industries using molding, by contrast, the tooling designers do not necessarily understand conformal cooling. Therefore, Linear uses the capability on its own behalf. Its injection molding facility, staffed by 21 people and running 3 shifts, largely serves non-automotive customers. Molding is commodity work, but Linear is able to use conformal cooling as its secret weapon. Adding its own 3D-printed conformal-cooled inserts to its tools allows this molding facility to deliver lower prices for the same molding work compared to competitors.
•Polymer Additive Manufacturing
Linear invested in HP machines as a mold-free alternative method of providing prototype parts. The HP model 4200 Multi Jet Fusion machines are aimed at "production," he says, but that word means different things in different contexts. Production in the automotive territory where Linear lives represents part quantities far beyond what 3D printing can serve, but the number of pieces needed in a prototype run equates to what might serve as production in much narrower markets.
The advantages he sees in 3D printing over moldmaking are these: "You seem to get paid faster for making parts than you do for making the tooling that makes the parts. Plus, if you need to fix something, it's not three guys working all weekend." If a printed part is unsatisfactory or faulty in some way, the solution instead is simply to change the CAD file, run the print job again and walk away.
过程知识
With the polymer 3D printing, as was the case with metal 3D printing when Linear first adopted this, there is a learning curve. How to nest parts and set printing parameters in Multi Jet Fusion so that a particular build is successful requires experimentation, and — again, like metal — the knowledge that figures into this experimentation and process development is becoming Linear's specialty.

Linear's team built this set of parts to illustrate the type of quantities Multi Jet Fusion easily makes possible. This batch of 120 parts was 3D printed in about 16 hours.
他指出:“利润很好,这是一件好事。正确的构建有时可能需要时间。”
But knowing how to get it right is also a basis for growth, and it is what helps to make Multi Jet Fusion the most scalable part of Linear's business.