Should You to Continue to Outsource Passivation?
Considering the growing acceptance of citric passivation, shops might find bringing this process in-house can lower manufacturing costs and speed delivery lead times.
#columns
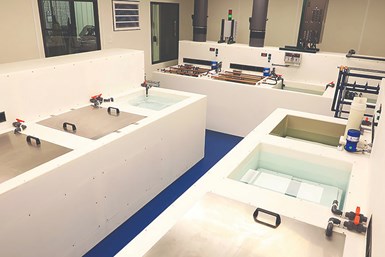
The medical industry’s shift from nitric- to citric-based passivation is spurring machine shops such as Complexus Medical to bring that finishing process in house. Photo Credit: Complexus Medical
It sometimes makes sense for shops to outsource ancillary production processes required to complete the manufacture of parts to trusted vendors while focusing on what they know best — precision machining. In some cases, though, bringing select processes in-house might enable shops to lower production costs and shorten delivery times while ensuring quality.
The latter has beenComplexus Medical’s experience.
Featured Content
印第安纳州,米沙沃卡运营合同制造商的complex orthopedic instruments brought in two processes that it previously outsourced — passivation and electropolishing. Michael Behrens, who in 2016 took over for his father, David, as company president, points to a few reasons for this. “Passivation represented one of our company’s highest spends,” he explains. “We were also driving to our passivation as well as electropolishing and heat-treating vendors an hour away upwards of three times a day. So, for cost reduction and faster lead times, we brought passivation and electropolishing in-house. We’ll continue to outsource heat treating because we simply don’t have room for it, and adding it doesn’t make sense, given our facility is temperature- and humidity-controlled.”
But what really prompted the addition of passivation is the medical industry’s shift away from nitric- to citric-acid-based processes for orthopedic devices. “We’ve wanted to bring passivation in-house for the longest time,” Behrens says. “However, nitric acid is terribly corrosive and damaging to machine tools. It wasn’t worth the risk or hassle. On the other hand, citric passivation is much easier to work with and is about as corrosive as orange juice.”
For cost reduction and faster lead times, Complexus Medical brought passivation and electropolishing in-house.
Complexus Medical purchased the passivation and electropolishing systems from Jacob Hay Co. in Wheeling, Illinois. Per environmental regulations, the shop had to construct a dedicated room for the equipment that could contain a catastrophic failure in case all processing tanks were compromised. This room required significant ventilation capacity, too. But it found that the ventilation system was removing too much of the conditioned air in the facility. As a result, the shop had to install a makeup air system that added 20 tons of air conditioning capacity to even out what the ventilation system was pulling in. Complexus Medical also added an air lock, because the ventilation system was pulling in pollen, mold spores, mosquitoes and other contaminates from the outside when the building’s overhead door was open.
Each process also required customer validation. For passivation, this included boil, copper sulfate, salt sprays and similar tests to determine that the process was removing all free iron from the surfaces of stainless steel parts. For electropolishing (which positively charges a part in an electrolyte to remove material peaks to smooth the part’s surface), a number of samples are processed to determine that a given power setting will repeatably remove the same amount of material. This is especially important for press-fit parts such as pins that must precisely fit mating holes.
The passivation and electropolishing systems were installed in 2019 so that validation could begin to bring them online in 2020. Behrens believes they will help position the shop to accommodate further growth, and it might start winning new business from unexpected sources.
“Until recently, if you were a supplier like Complexus Medical and weren’t already on a medical OEM’s approved supplier list, that company wouldn’t even take your call,” he explains. “But it seems consolidation among contract manufacturers in the orthopedic industry has prompted the OEMs to begin considering new vendors, especially for complex instruments.”
RELATED CONTENT
Boning Up On Thread Whirling's Advantages
螺纹旋转的附件安装在骨头上screw maker's Swiss screw machines prove to be just the right prescription for the company's mix of screw sizes and run quantities.
Forming Hex Holes For Bone Screws
Close tolerances and quality surface finish are critical in successful medical machining. To meet such requirements in broaching titanium and stainless steel bone screws, with machined depths ranging anywhere between 0.080 and 0.150 inches, Hassay Savage Company (Turners Falls, Massachusetts) has recently developed an indexing-broach process using four-point or two-point punch broaches for use in Swiss-type CNC lathes.
Advancements in Thread Whirling Tooling Technology
Many understand the advantages of thread whirling on a CNC Swiss-type. However, new tooling technology for this thread-machining process can further improve cycle times and reduce cost per part.