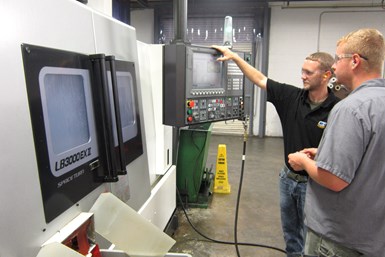
每个工作日下午3点左右,定制工具店的工作人员开始建立车削中心,在晚上通宵工作。
对于杨氏兄弟来说,车间自动化开始于在现有的数控车削中心上增加一个料棒给料机。
这发生在吉伦和鲍勃·杨买下田纳西州的库克维尔后不久,自定义工具在2008年。(吉伦是总裁;鲍勃是副总裁。)送料机使一个两轴CNC车削中心能够在有员工的日子里无人值守地长时间运行,与公司以前的管理方式相比,它代表了车间文化的重大转变。也就是说,在业务收购之前,即使工资支票仍然是手写的,也从未考虑过将手动任务自动化。
今天,已经实现了各种自动化示例,并且商店以各种方式从中受益。例如,两个新的带子主轴的杆进给y轴车削中心、活动模具和零件收集器可以在一夜之间运行,目标是加工零件,同时在车间没有人员的15.5小时内获得尽可能多的生产时间。车间员工(许多人现在不再只是简单地装卸机器)能够更好地考虑并提出改进流程的方法。通常,这些有用的建议与自动化现有的手工任务有关(例如将零件去毛刺集成到加工周期中)。此外,新的检测技术已经实现了对连夜加工的多个零件的自动化测量。
Custom Tool最近还为其大约10年前建立的“生产日志”计划策略自动化了数据收集。生产日志已成为其运营的支柱,它揭示了车间机器在一天中相对于预期日产量的效率,并显示了车间占用了多少“被盗时间”。(这是兄弟俩对每晚15.5个小时无人值守的昵称。)它还有助于确定适合通宵生产的工作,因为该车间希望将年度熄灯加工时间的百分比提高到其总产量的50%或更多。正如Bob所说,这种无人值守的加工时间相当于第二次员工轮班,成本要低得多。
给料机后
Bob Young管理网站运营,而Gillen(他也担任AT&T咨询公司物联网解决方案的首席架构师)位于乔治亚州的亚特兰大(尽管他会在时间允许的情况下经常去商店)。两人决定购买定制工具后,鲍勃,谁曾在机床经销商,接近退休的前业主,并寻求退出。
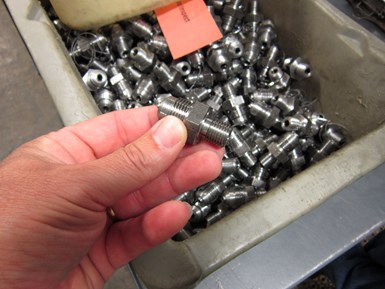
这个燃料装置是该店第一项通宵无人值守的工作。它在两个螺纹操作中使用了多余的工具来补偿工具磨损,并将可加工的零件数量增加了一倍。此外,自拍摄这张照片以来,该店已开始使用一种特殊工具进行循环去毛刺,以消除二次手动去毛刺操作。
兄弟俩立刻意识到,改变公司文化至关重要。两人开始努力灌输一种持续改进的心态,着眼于尽可能多地实现自动化。考虑到一些自然的人员流失,他们雇佣了一些新人,其中许多人相对年轻且缺乏经验,他们更愿意接受先进技术,也更倾向于提出简化流程的方法。
在看到第一个杆料车削中心的无人看管的加工优势,并预见到熄灯加工将成为现实的时候,自定义工具公司在2012年进行了更大的投资,增加了一个y轴大熊町LB3000 EX Spaceturn与活工具,一个子主轴和一个边缘技术棒材给料机可完成部分零件的加工。该店在2016年又增加了一台这样的机器,2019年1月又增加了第三台。
也就是说,熄灯加工的好处是需要时间的。车间必须熟悉新设备,并验证潜在的夜间加工操作。然后,它开始将工作时间越来越长,一直持续到晚上,直到车间完全有信心能够成功地运行一整晚。在建立可靠的无人值守流程时考虑了几个因素,该车间在此过程中吸取了许多经验教训。其中一些涉及:
- 冷却系统。冷却液压力意外下降或冷却液输送中断可能导致工具断裂。夜间运行的机器比只运行一班的机器需要更多的维护。因此,如果一台机器运行一个班次,增压泵过滤器通常每隔几天检查一次,那么该过滤器现在必须每天检查一次。此外,定制工具的第二个y轴车削中心设有一个控制器,如果它检测到冷却系统有问题,就会发送信号停止机器。
-
正如鲍勃·杨向高级编辑洛里·贝克曼解释的那样,在开发熄灯加工工艺时,考虑芯片管理是很重要的。该单元具有输送带齿,使其能够更好地处理长,串铝芯片时,车削中心运行无人值守过夜。
- 收集部分。最初,芯片料斗也作为零件收集器。现在,每个车削中心都有一个集成的零件收集器。收集器的尺寸必须能够适应隔夜的产量。如果产能太小,那么一夜之间可以生产的大零件的数量是有限的。此外,冷却液随着每个被收集的零件一起流出,因此需要某种方法将冷却液从零件收集器排出并返回到机器的水槽中。
- 条支线。如果零件的工作是相当大的,一个棒材给料机的能力可能会限制多少零件可以在一夜之间加工。另一方面,如果循环时间非常快,就有可能消耗掉所有装载的barstock,这意味着必须有人来车间补充材料,这样隔夜的零件产量才不会减少。
- 多余的工具。如图所示的带有两种螺纹的燃油配件部件是自定义工具使用冗余工具设置的第一个作业。当该作业有操作人员在场时,由于工具磨损,操作人员可以判断何时需要改变偏移量。然而,该车间发现,由于需要对两个螺纹工具进行偏移调整,最初只能运行4个小时。认识到这一点,该车间开始使用冗余的螺纹工具,在刀具磨损成为问题之前,在特定的零件数量上要求更换刀具。尽管该车间并没有从其螺纹工具插入中获得所有潜在的寿命,但机器可以在无人值守的情况下运行的额外时间证明了这一点。
- 负载监控。有了主轴载荷监测功能,当载荷为零时,就意味着工具坏了。零件程序的编写使机器在这一点停止,而不是继续运行作业,冒着损坏后续工具的风险。
- 测量能力。当数百个零件可以在一夜之间加工时,这是很好的,但无人值守的生产已经改变了一些定制工具车间员工每天开始的工作。必须为零件分离、检查、机器评估和下一项工作的准备留出时间。事实上,在该厂第一次实行熄灯生产时,零件检验就成了瓶颈。为了加快检查的速度,自定义工具增加了一个日本基恩士IM系列图像尺寸测量系统,可以自动测量和记录设置在设备上的一个或多个部件上的众多外部部件特征。
自动化生产日志记录
Bob在2011年实施的生产日志,通过将车间的9台数控机床和1台机器人焊接单元的日常计划工作与实际产量进行比较,揭示了它们每天的生产效率。它还揭示了商店如何有效地利用可利用的夜间时间。
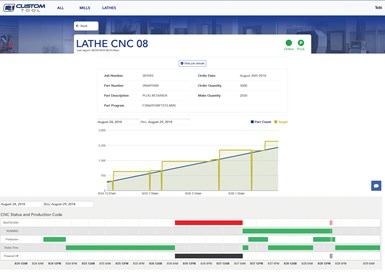
自动数据收集系统每20分钟从机器上收集一次生产信息。它还从车间的ERP软件中提取工作数据。然后可以创建报告,以更图形化地显示生产日志信息。图片来源:自定义工具
直到最近,所有这些数据都是手工收集的。每小时,员工记录每台机器的零件生产数量,并将这些数值和机器状态代码输入到生产日志电子表格中。该店力求最大化代码10和15的值,分别代表该店单日班的生产时间和夜间无人值守的生产时间。Bob说,将这些值与预期的日产量进行比较可以揭示真实的机器利用率。其他代码,如安装、返工和等待材料、工装或操作员注意的时间,除了实际加工时间外,还阐明了完成一项工作所需的确切时间。
已经设置了公共变量来跟踪每个作业的状态。零件计数由G代码处理,每完成一个零件循环就增加一个。其他变量需要运算符输入。其中包括运行目标(当零件数量达到该值时,机器将暂停)、作业编号(列在作业旅行表上)和生产日志代码(显示生产状态何时发生变化)。
生产日志有助于识别适合熄灯操作的进程。如果设置为整夜运行的机器没有接近15.5小时的可用时间,那么这个作业可能不太适合整夜运行。或者,如果一台机器运行了整个晚上,而另一台机器运行了半个晚上,那么将只运行了半个晚上的作业推到另一台机器上,用另一台运行时间较长的机器上的工作替换它,以实现更高的利用率,也许是有意义的。生产日志也可以作为一种日志,因为它用于记录导致机器达不到目标产量的工具破损或送棒器故障等问题。
该车间继续朝着这样的场景努力,即没有人需要每小时访问机器来为生产日志收集和输入数据。这要归功于Gillen正在开发的自动化数据收集和报告系统,该系统使用基于web的工业物联网(IIoT)平台,从具有开源MTConnect通信协议代理的机器中提取数据,以及该公司的Jobboss企业资源规划(ERP)软件。这个平台是Devicewise for Factory fromTelit该公司提供工业物联网模块、软件和连接服务和软件。
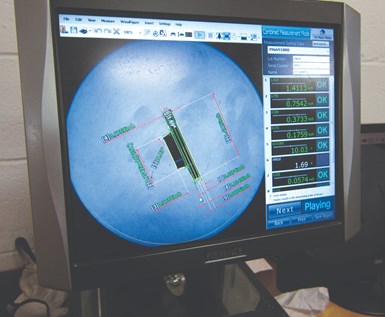
熄灯加工意味着很多零件在等待车间人员早上到达。对于定制工具,这造成了检查瓶颈,促使车间增加了图像尺寸测量设备,以加快质量控制人员的零件测量速度。
吉伦说,这个系统的好处是它与各种控制器接口,不需要定制的编程来收集数据。它被配置为自动从机器上手动收集的所有数据(零件计数、机器代码等)以及ERP数据(作业编号、工作描述、订单日期、订单数量、交货日期等),并将其存储在云中。数据可以通过网络仪表板访问。然后可以创建报告,以更图形化地显示以前在生产日志电子表格中可用的内容。
自2018年6月初以来,系统每20分钟收集一次数据,没有遗漏正在运行的机器的条目。吉伦说,市面上有很多好的机器监控产品。然而,他的技术背景提供了一个探索内部解决方案的机会,该解决方案解决了商店最感兴趣的业务信息。他还认为,这种数据收集能力还可能导致更高级的分析,例如将切割时间与特定类型的切割工具或刀片联系起来。
相关内容
移动到数控瑞士螺丝机
在18个月内,三台新的CNC瑞士机床为这家伊利诺伊州的商店提供了真正的增长。
如何从瑞士型和多任务机器获得更有效的生产
SolidCAM用于多轴瑞士型和多任务机器,提供了非常高效的CAM编程过程,生成最佳和安全的铣削程序,极大地提高了铣刀寿命。
瑞士机械加工趋势
这家佛罗里达医疗制造商是在CNC瑞士机器上生产复杂医疗部件的专家。他们的车间已经从18名员工发展到135名员工,为苛刻的医疗行业高效地生产小而难的零件。展望未来,这家店的联合创始人只看到了更好的未来。