维氏工程到处都是机器人。其中许多体型庞大,力量强大,大多数移动速度快得令人眼花缭乱,扮演着单一的角色,目的如此单一,进入它们的保护笼子需要严格遵守严格的安全协议。除了最新的协作臂的优势,高零件量,快速的生产速度,充满诱导磨损冷却剂和油渣的环境,使得传统的机器管理自动化成为这家一级汽车制造商的唯一选择。
然而,维克斯的成功在很大程度上是由于实现了工业机器人可以比许多人认为的更多功能的想法。也许最好的证据是靠近车间中心的一个相对较大的建筑,上面装饰着一个醒目的标志:一只红兔子。
在里面,一个机器人悬挂着,操纵着三个hmc的墓碑固定装置和一个辅助压压站的工作。六轴工业臂在工作区中自由移动,没有电气柜、控制器和其他必要的组件,所有这些都安装在屋顶上。以太网电缆、传感器连接和其他必要的电线蜿蜒穿过框架的空心钢焊接,在视线之外。如果工作干了,整个系统可以移动到一个新的位置,并适应新的工作与模块化组件,如可重构的零件抽屉和进料/出料系统。
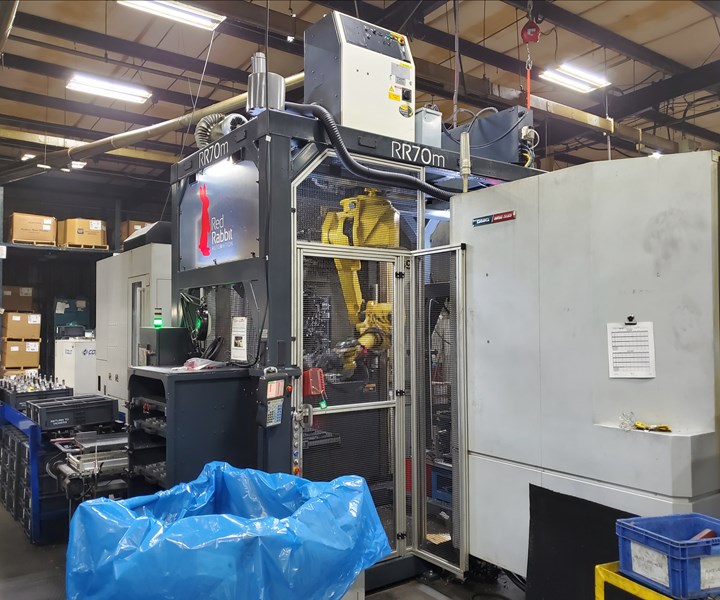
自动化主管罗伯特•克拉克(Robert Kracker)强调,将机器人放入框架中并不一定会使重新部署机器人变得容易。然而,这确实比从零开始更容易。使工业机器人更容易部署和重新部署有助于降低自动化的总体成本,并尽可能地节省大量的前期设计和实现成本。他说,下次Vickers得到一份新合同时,几乎肯定会采取同样的做法。
事实上,他和他的团队已经组装了他们所谓的可重新部署机器人的五种不同配置,只是不在他们自己的车间里。帮助其他类似的企业应用类似的系统是一个新的支线企业的工作,赤兔.通过这种方式,维克斯扩大了对内部自动化专业技术的投资,就像扩大了对自动化本身的投资一样。
焦点数控加工
在自动化集成的行话中,“红兔子”指的是用来测试系统的故意出错的部分。克拉克说,那些不懂这个术语的人很可能是这项新业务的理想客户(假设他们的工作证明了工业机器人的合理性)。
这些理想的客户也往往看起来很像维克斯,或者至少是维克斯可能的样子,如果公司没有那么早地高度关注自动化的话。这里的人知道“红兔子”这个词,因为早在15年前该公司安装第一台机器人之前,内部工程团队就已经定期进行这些测试。克拉克说,在没有新的或正在进行的项目的情况下,帮助其他人在更短的时间内完成同样的旅程,提供了一个从自动化集成专业知识中受益的机会。
“我们是一个自动化集成商,我们的DNA中含有机械加工。——罗伯特·克拉克
目前,维克斯和红兔的工程团队是一个整体,尽管有些团队更专注于一个实体,而不是另一个实体。然而,这家附属企业已经发展到现在在密歇根州奈尔斯(Niles)拥有自己的工厂,距离维克斯在新特洛伊(New Troy)的12万平方英尺工厂只有几英里。自2017年底正式推出集成服务以来,克拉克表示,在外部应用程序方面的工作增强了他的信心,认为该公司提供了真正差异化的服务。他说:“我们是一家自动化集成商,我们的DNA中含有机械加工。”
自动化开始领先
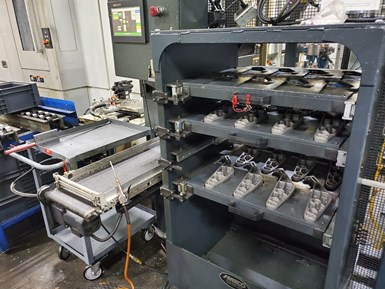
可加工的顶板使得第一个系统的装载抽屉相对容易重新配置,以适应维克斯的新工作。其他系统也可使用视觉引导的箱子选择。
克拉克说,红兔的模块化机器看护系统是多年来简化电池设计和实施初始阶段的努力的体现。尽管配置和应用差别很大,但所有的独立系统都有笼子、电气箱、控制箱和机器人。其他可用的模块可以根据需要混合和匹配,包括用于拣箱的视觉系统以及用于零件吹除、研磨、抛光、去毛刺或其他辅助应用的工作站。提前配置这些元素,使它们一起工作,并将它们合并到一个单独的、自包含的单元中,可以为新项目提供一个良好的开端。它还使重新部署变得可行,而不管是否需要重新部署。
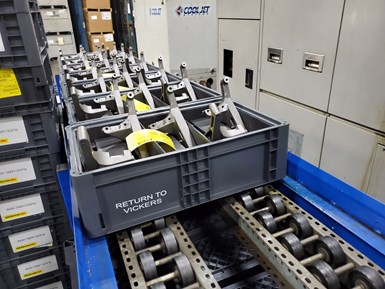
加工后,铸造支架离开系统上的出口输送机。
维克斯公司车间里的系统是第一个建成的。它在第一次申请时就面临了第一次考验,那是一份油田零部件合同,但在组装过程中失败了。最初设计的管状组件在三台车床上生产,该系统被重新配置为铸造汽车支架。
新的几何结构需要新的机器人抓手,所有车站都需要新的固定装置和新的编程。尽管如此,Redployable Robot还是证明了它的价值。“如果我们用老方法来做,我们就必须把机器人放到位;把抽屉放好;为电器柜和机器人控制器柜找个地方,甚至可以移动车床;而且线路连接也会乱成一团,”克拉克解释说。
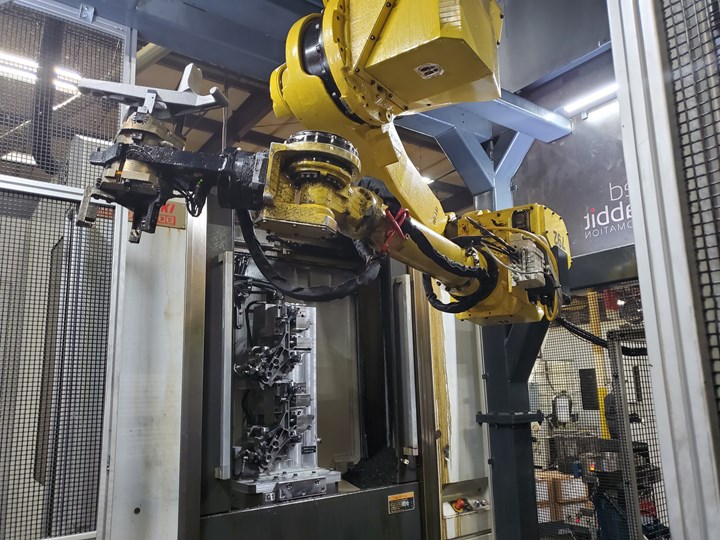
与传统的底座安装相比,倒挂机器人有助于节省地板空间。两支臂是可用的:FANUC 710,提供70公斤有效载荷,和FANUC M20iB,提供25公斤有效载荷。
(半)组合式机器养护
另一种重组可能以同样的方式完成,其浪费要远远少于该过程所带来的浪费。作为一个额外的好处,该系统被认为是一件设备的折旧目的。无论如何,他强调,重新部署可重新部署机器人不是一项可以掉以轻心的工作。最适合多年的零件合同,这是工业自动化的任何定义,不同的应用程序面临不同的挑战,甚至在同一车间。他说:“在实现工业自动化方面,你只能标准化这么多。”
一个在计划的最后阶段的项目现代机械厂对维克斯的访问就是一个很好的例子。这个四台机器的单元将加工21个不同的零件,其中一些将从车床送棒器进入,另一些将在视觉系统的引导下从箱子中机器人采摘。所有的零件都在车床上进行车削,大多数也通过由同一机器人服务的VMC。然后,机器人将部分加工好的工件放置在一个再加工工位上,由第二个机器人拾取,后者将通过一个或两个单元的研磨机对其进行操作,然后将其放置在一个输出输送带上。
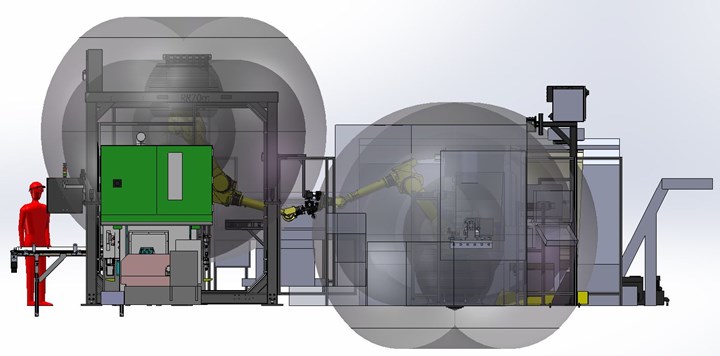
起初,该单元似乎是两个相邻的可重新部署机器人的理想选择。然而,更深入的研究表明,达到的限制将使这种方法不切实际。充分利用垂直空间的一个代价是有限的延伸范围,特别是在机器人活动范围的低端。在这种情况下,悬挂在框架上的机器人将无法到达中间的重定向站。在这种情况下,简单地将设备安排得更近一些,使重新抓取站在可触及的范围内,将不可能清洁车床的冷却液盘(并且,如下图所示,将机器人放置在靠近工作站的地方也可能需要解决问题)。因此,集成商和客户选择了一个更传统的,安装在基座上的机器人在电池的那一边。
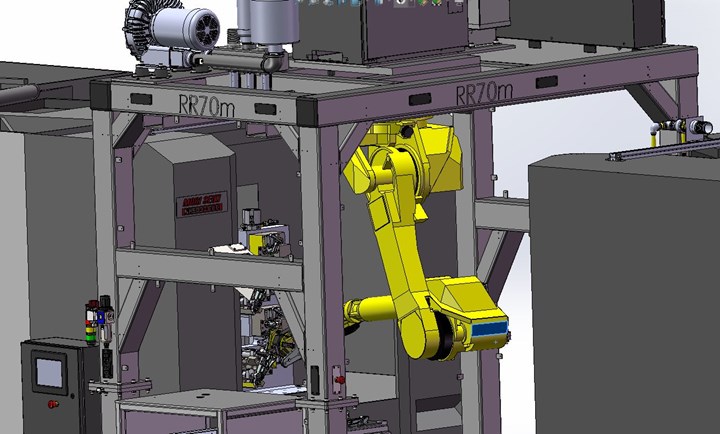
倒置机器人的第三个关节,如图所示,是一种常见的解决方案,因为机器人被放置在靠近机床的地方。