Continuous improvement has always been critical toSchmid Tool and Engineering (STE)in Villa Park, Illinois. That’s why its management knew when it was time to hire an outside professional to help the team implement some lean manufacturing principles. Doing so enabled the team to pinpoint processes that could be improved in its business that supplies parts to the firearms industry. After the company implemented twoHydromat Inc.rotary transfer machines, it experienced an increase in its on-time deliveries rate, a reduction in its scrap rate and a reduction in its backlog.
When the family-owned company hired Erik Poulsen (who had 21 years of experience in precision machining) as the director of operations, he voiced concerns about the way the hammers and triggers were being machined after he built a value stream map. The map’s resulting information was used to identify where to maximize value and minimize waste throughout the business.
Featured Content
At that time, the parts were manufactured on dedicated custom rotary index machines and secondary operations. Poulsen was bothered by many inefficiencies this process caused, including multiple part fixturing, high scrap rates, part family scheduling issues, machine reliability, changeover complexity, quality standards, downtime, maintenance and more.
他将这些问题带给了Ste的所有者Eric Schmid和Heidi Schmid Schaefer。他们允许Poulsen及其工程师团队探索锤子和触发细胞的新制造选择。
家庭遗产
In 1943, Gustav K. Schmid, an immigrant from Germany, opened a small tool and die shop in Chicago, Illinois. Over time, STE developed into a full-service CNC contract machine shop specializing in machining small castings. Today the 3rd generation owners of the shop, Schmid and Schaefer, are the grandchildren of Gustav Schmid.
Michael Mechnig, manufacturing engineer technician, adjusts the EPIC HF program on one of STE’s indexing chuck machines. Photo Credit: Hydromat Inc.
Following almost 80 years of machining parts for military, firearms, vending machines, exercise equipment, recreational vehicles and medical industries, the majority of its business today is dedicated to the firearm industry.
Choosing the Right Solution
Experienced in the precision machining industry, Poulsen knew the solution to the company’s inefficiencies would be to integrate a rotary transfer machine. After receiving numerous quotes from several rotary transfer manufacturers, the STE team opted to invest in twoHydromat Epic HF HS-16indexing chuck machines. “When it came down to choosing between rotary transfer machines, we moved forward with Hydromat because of its location, level of quality and specifically its level of service,” Poulsen says.
Hydromat worked closely with the Schmids and the rest of the STE team to provide a turnkey system fit to their needs.
Applying the Technology on the Shop Floor
到2021年12月,新的扶轮转移机器were delivered to the company, and accommodations were made to implement the machines on the shop floor. In comparison to its existing knowledge of CNC machines, the Hydromat machines’ level of complexity meant more moving parts than the company was familiar with. But STE simplified the approach to learning the new technology and viewed the machine as what it is – 16 spindles or 16 individual machines in one.
“We had a slight learning curve to overcome, but nothing significant we couldn’t handle with the help of Hydromat support,” Poulsen explains. “We have now trained our machine operator and two night lead associates on how to run the machine and complete changeovers.”
The engineering team has since come to learn the machine and how to modify programs. It has changed the tool path to clip-off burs and driven down the cycle times.
Flexibility Increase and Waste Reduction
Prior to implementing the rotary transfer machines, STE did not have the option to complete changeovers due to the reliability of the manufacturing cell. Their previous custom rotary index machines were dedicated machines, which led to many scheduling issues. This caused problems when trying to meet the production requirements of each part in the hammer and trigger part families.
But now with the new machines, the hammer and trigger cells are hitting their production goals. In fact, the company has increased on-time delivery by 85%, reduced scrap rate by 98% and cut its previous backlog by 90%.
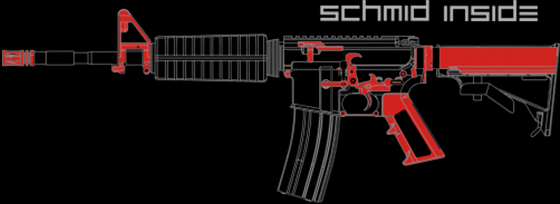
This diagram displays AR-15 firearm parts manufactured by STE. 70% to 80% of AR-15s in the United States include Schmid products. Photo Credit: Schmid Tool and Engineering
“Before January (2022), we ran 40,000 units between the two Hydromat machines and only scrapped 24 units,” Poulsen says. “The two machines have brought many improvements to the Schmid manufacturing process: minimum downtime, increased quality, repeatability, flexibility, ease of scheduling part families and quick changeovers.”
通过在机器两上产生三种锤子和四个变体的锤子变体,该公司可以快速有效地生产这些零件。
“Depending on the complexity, our changeovers range from 30 minutes for program changes or approximately one hour for changing out chuck jaws,” says Paul Calzaretta, manufacturing engineering manager.
New Business Opportunities
Now that STE has increased its production and quality, the company wondered how it could take steps to increase brand recognition and brand loyalty by selling products directly to dealers and firearm shops. Hence,里面的schmidwas born.
Erik Poulsen, director of operations, and Paul Calzaretta, manufacturing engineering manager, stand on the EPIC HF HS 16 indexing chuck platform. This is STE’s one of two production cells producing a family of parts on Hydromat machines. Photo Credit: Hydromat Inc.
Ste由Ste生产的产品的直接B2B店面和产品来源包括其Gun Nuts产品线和其他批量和零售包装的商标内部产品。
STE also launched theWee1Tactical JR-15 rifle, which is a .22 caliber long rifle. This smaller rifle was created to develop a line of shooting platforms that will safely introduce small stature shooters to shooting sports, the company says.
The company is currently working on the smaller fixturing required to produce this new rifle’s trigger and hammer parts on its Hydromat machines.
Read: As a Business Evolves, So Does its Machining Technology
Hydromat Inc. |hydromat.com
Schmid Tool and Engineering Corp. |schmidtool.com
相关内容
Saving Lives with a Net
Every day, metalworking manufacturers contribute to the general and specific welfare of our nation’s economy by adding value and creating wealth. This New Hampshire shop has the added distinction of helping save the lives of our combat troops.
Rotary Transfer: Turning Up the Volume
This contract manufacturer set its sights on high volume, precision turning and assembly of complex components from Day 1 and continues to succeed in a market many have abandoned using CNC rotary transfer machining.
Rotary Transfer Versus Swiss for Small Precision Parts
A little creativity goes a long way in meeting the challenges that this high-production application presents.