Eaton Corp.使用3D打印系统制造的零件
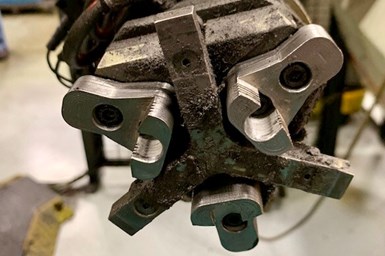
This 3D-printed stainless steel robot gripper is used to automatically load a gear hobbing machine so it can perform a gear chamfering operation. Eaton Corp. saw a 90% cost savings by using Desktop Metal’s Studio System compared to using traditional subtractive machining to create this gripper. Photo Credits: Desktop Metal
Like many other automotive suppliers,伊顿公司’s Industrial Sector, Vehicle Group, endeavors to minimize downtime on its tooling and fixturing manufacturing lines to keep up with the rapid iteration of vehicle design and the worldwide demand for automotive parts. Besides mass production, the company also produces one-off, custom solutions for customers around the globe.
Therefore, figuring out how to best retool manufacturing lines quickly and efficiently was a priority, but it also strived to develop and prototype custom parts for transportation challenges fast and proficiently. To do so, company engineers turned toDesktop Metal’s original Studio System — a metal 3D printing system designed for an office space that includes three separate pieces of equipment: the printer, debinder and furnace.
Featured Content
The Studio System’s impact at Eaton was immediate. With the ability to quickly print a variety of tooling and fixtures — from a complex set of pneumatic jaws used in a gear chamfering process to relatively simple press tools — engineers were able to cut the lead time for tooling by more than 60%. Lead times went from three to four weeks to only five to 10 days.
Also, depending on the size and design complexity, printed tools are, on average, between 40% and 80% less expensive to manufacture compared to using subtractive or traditional manufacturing.
In addition, company designers can use additive manufacturing to explore new levels of design complexity and create parts that include internal channels.
由于能够更快地满足客户需求并快速迭代零件,因此该系统现在已成为工程和工具室团队的工作流程中的标准配置,并每天用于支持全球的操作。
“Before additive manufacturing, I was afraid to fail,” says Alex Abernethy, senior engineer at Eaton Corp. “After additive manufacturing, if you fail it happens quickly, and you can correct the error more quickly.”
Though Eaton had years of experience using polymer printers, the company began searching for a metal 3D printing system that could support its shop floor. The company chose to invest in the Studio System due to its ability to significantly reduce the cost and lead time to produce tooling and other parts, as well as its ease of use and office-friendly design. Because it uses no loose metal powders or dangerous lasers, operators don’t need personal protective equipment.
Desktop Metal calls its additive technology Bond Metal Deposition. BMD is a metal additive manufacturing process that uses bound metal rods made from a combination of metal powder and a wax and polymer binder. In the BMD process, these filament-like metal rods are fed through a heated extruder onto a build plate, layer by layer, until a green part is built.
Then, as the second step in the company’s original Studio System 3D printer, the green part is placed into a debinder, where a fluid dissolves the primary binder in preparation for the third step — sintering. The system’s sintering furnace, which works like a traditional sintering furnace used in powder
“Before additive manufacturing, I was afraid to fail,” says Alex Abernethy, senior engineer at Eaton Corp. “After additive manufacturing, if you fail it happens quickly, and you can correct the error more quickly.”
metallurgy processes, finishes the debinded part. This is the system used by Eaton, but Desktop Metal’s latest technology eliminates the need for a debinder (more on that later).
由于能够快速满足客户需求的速度并迭代零件,因此该系统现在是工程和工具室团队的工作流程的标准部分,并每天用于支持世界各地的运营。该系统已经变得如此成功,以至于伊顿现在正在探索投资生产零件的粘合剂喷射技术的想法。
原来的工作室系统是一个由三个步骤组成的3 dting system which consists of the printer, debinder and a furnace. This is the system that Eaton used, but the latest technology from Desktop Metal eliminates the need for a debinder.
伊顿(Eaton)使用工作室系统打印的零件分为四类:抓地力,组件,测试固定装置以及工具和更换零件。
- Gripping Components.由于其许多传统的机床全天候运行,伊顿工程师努力提高其生产率。一种方法是自动化一些过程,包括使用机器人臂和定制抓手在装载和卸载过程中保持工件。印刷夹具导致减少制造业时间和零件成本,同时减少了传统制造方法的后勤和运营商负担
- 测试固定装置。The Studio System also proved to be an effective tool for producing custom fixturing. Before shipping products to customers, Eaton conducts regular tests to ensure its products meet stringent standards and work as intended. Many of those tests demand unique fixturing, which is almost always produced in low volume. Printing those fixtures using the Studio System has been a value-added process, enabling the company to save both time and money, and reduce the logistical burden associated with traditional manufacturing methods and supply chains.
- 工具组件。Many high-volume manufacturing processes rely on hard tooling, which are generally among the more expensive and time-consuming parts to produce. By printing that tooling using the Studio System, Eaton has reduced lead times and costs for these tools.
- Replacement Parts.As with other manufacturing facilities, Eaton must constantly maintain its equipment and replace parts as they become worn or broken. To avoid extended periods of downtime while waiting for replacement parts, the company must either keep many replacement parts on hand or pay a premium to have the parts made quickly via traditional methods. The Studio System, however, offered another option. Using 3D scans of parts, Eaton engineers were able to reverse engineer models of several parts where drawings were not available and adapt existing designs for printing. Using the 3D printing system, the company was then able to produce replacement parts in days, which is much faster than traditional manufacturing. The printed parts were also up to 90% less expensive than their traditionally machined counterparts.
From 3 Steps to 2 Steps
Desktop Metal’s latest metal 3D printing system, Studio System 2, includes only the printing and sintering processes with a software-controlled workflow. New material formulations enable printed parts to be placed directly into the furnace, without the need for the typical solvent debind phase.
借助公司的制造软件(录音室系统2本人),零件创建的所有方面都是自动化的。该公司表示,该软件会自动扩展该零件,并为印刷和烧结过程提供可分离的支持,并应用专家冶金库来优化制造。
The Studio System 2 also automatically generates seams throughout support structures and prints a reformulated ceramic interface material between the support structure and the part, enabling parts to easily be removed by hand.
该技术还使用户可以通过按下按钮来更改打印头,并在打印作业期间使用可重新填充的墨盒系统快速更换材料。
相关内容
Rotary Transfer Machines Help Shop Make Transition
Camcraft Precision Machined Components purchased two rotary transfer machines from Hydromat Inc. after winning a bid on an automotive plunger.
带有多主轴磨练系统的“孔”新球赛
Automating the honing process is key to high-volume precision bore production with sub-micron accuracy.
Chip Control Solution Provides Increase In Tool Life
Replacing the traditional ISO-style inserts with a reaming system solved a chip buildup problem in bore finishing of injector bodies.