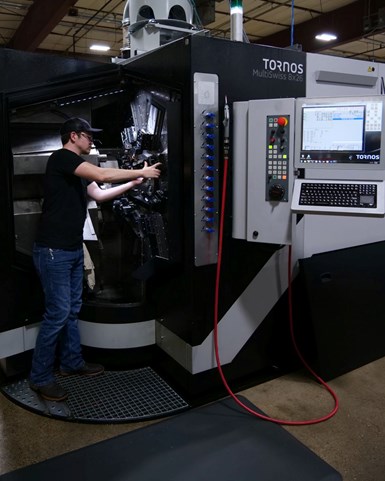
As a job shop, Mitotec Precision continues to identify ways to speed changeovers for jobs that run across its two CNC multi-spindle machines for operators such as apprentice-now-employee Trevor Hutchins. Batch sizes of 20,000 parts is its sweet spot for these machines. (Photo Credit: Mitotec Precision)
Mitotec Precisionis no stranger to multi-spindle cam automatics, but is new to CNC multi-spindles having purchased its first one in 2019 (added a second in the spring of 2022). What’s interesting is the Necedah, Wisconsin, company has never used its traditional cam or more recent CNC multi-spindles as one might expect for these types of high-production machine tools.
“We’re a job shop,” explains Clinton Pouillie, general manager. “Although a multi-spindle machine conventionally might be dedicated solely to running one part or a family of like parts, we’ve found a way to make 20,000 parts per run work for us despite the changeover times.
Featured Content
“In considering this, we first asked what we are as a company,” Pouillie explains. “If we are a multi-spindle company, then that’s where we need to make our capital investments. We also considered how this could help mitigate the challenge of finding new team members as the machines can match the output of four single-spindle machines that might require multiple operations as well as boost overall production compared to those machines.”
But even beyond the higher production capabilities, a CNC multi-spindle would offer the opportunity to respond faster to customers’ shrinking lead times/hot jobs that might be challenging to deliver on multiple single-spindle machines. In addition, it would create a single quality stream of machined parts to inspect rather than many streams from different machines.
I learned more about this during a recent visit to the 80-person, ISO9001-2015-certified shop that is now working to speed setups to minimize changeover times for its now two CNC multi-spindles, while facing a good challenge to have: endeavoring to keep them fed with new work given they might produce completed parts every 8 seconds.
New Identity, Direction
The first CNC multi-spindle purchase was on the heels of a business rebranding. Until late 2018, the company was known as Necedah Screw Machine Products. The name change to Mitotec Precision was made to demonstrate to customers and potential new employees its move away from mechanical machines to new CNC technology such as Swiss-types and turn-mills. (The company says the prefix “mito” means “threadlike” or precise and its pronunciation implies strength and might. The second half of its name represents the technical aptitude of its team.)
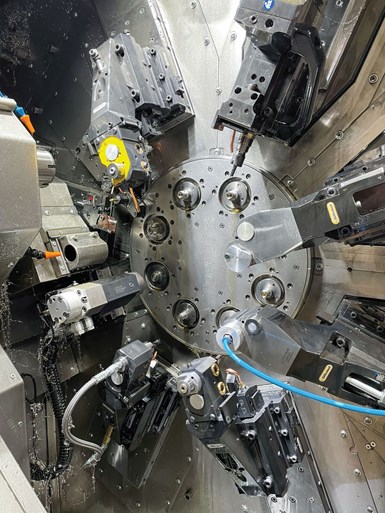
这家商店选择8-spindle机器26毫米barstock capacity believing this configuration offered the right combination of size and speed for the complex parts it would run across them. It is also in the process of eliminating external coolant lines, instead running oil through the tooling to further speed changeovers.
The CNC multi-spindle platform was the next logical step in terms of multitasking machining technology. After considering a few builders, the shop chose an 8 × 26 MultiSwiss fromTornos Technologies U.S. Corp.
Pouillie notes that Tornos offers its multi-spindle machines in a few different configurations. The shop decided that an 8-spindle machine with 26-mm barstock capacity offered the optimal combination of size, spindle speed (6,000 rpm) and spindle capacity to facilitate a broad range of complex parts and part sizes.
He also appreciates the machine’s hydrostatic spindle bearing design. “What impresses me is that the machine can be running eight 1-inch-diameter steel bars at 5,000 rpm and you hear the sound of the mist collector over any spindles noise,” Pouillie says, “We don’t hear vibration or rattling which leads to higher tool life, improved surface finishes and overall process stability.” Oil temperature control also contributes to process stability, while high-pressure oil delivery (the machine features 20-, 40- and 80-bar high-pressure coolant pumps) is very helpful in breaking chips and evacuating them from the cutting zone.
Pouillie says the shop uses TB Deco programming software from Tornos which he feels is particularly valuable for the multi-spindle platform. “The programming isn't as hard as one might think as each spindle has its own program, but it can be a challenge to coordinate wait codes without the software,” he explains. “Plus, it also automatically simulates a part run to reveal any error codes or overtravel conditions prior to running a job. In addition, it calculates the cycle time extremely precisely as it proves out a job.”
The TB Deco software also automatically adjusts an entire part program as a programmer makes changes to perhaps move operations from the spindle that has the longest cycle time (which on a multi-spindle is the true cycle time for the part) to another spindle(s). Mitotec Precision has an offline seat and its engineering team uses it to create all programs for the two CNC multi-spindles.
Currently, the shop is devising ways to reduce changeover times which for now stands at under 8 hours. Although that can be twice as long as setting up a single-spindle for a new job, the production speed of an 8-spindle machine makes up for that.
For example, it is machining channels on the side of itsGoeltenbodt夹持装置,与地面停止使交配fast changeover with high positioning repeatability. In doing this, each tool becomes dedicated to a specific spindle and there is no need to touch off cutters. The shop is also in the process of eliminating external coolant lines and instead running oil through the tooling to further speed changeovers by eliminating the need for operators such as Trevor Hutchins, shown in the lead photo, to remove and reclamp coolant hoses. Pouillie notes that the open design of the MultiSwiss provides Hutchins with easy access to the toolholders “without getting drenched in oil,” he quips.
Improved Customer Response
Mitotec Precision has run a number of jobs across its MultiSwiss machines and has been able to more quickly respond to customers’ hot jobs. “A customer might call needing 20,000 pieces of a complex part in a month, Pouillie explains. “Normally, this means we’d need open capacity on multiple machines, which we might or might not have. A multi-spindle gets us the ability to respond with one machine and one quality value stream for us to control.
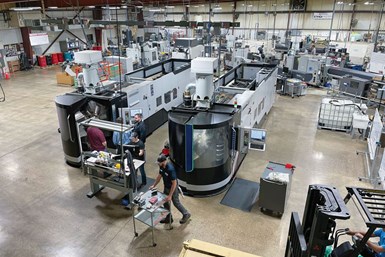
Mitotec Precision reconfigured its floor space to leave room on either side of its two CNC multi-spindles because it envisions adding more of these high-production machines as part of its business model moving forward.
The MultiSwiss also offers a safer chance to take on more work from one customer because the shop won’t have to tie up multiple single-spindle machines for just one customer. That doesn’t make good business sense. And now that the shop has two CNC multi-spindles, customers with jobs running on one won’t have to worry about their work not being completed on time if that machine goes down because the job could be easily transferred to the other.
Faster Production Ripple Effects
Although Mitotec Precision has benefited from the boosted machined parts production and other advantages the CNC multi-spindles offer, that higher production from two individual machines has caused bottlenecks with regard to part inspection and cleaning that it has worked to open.
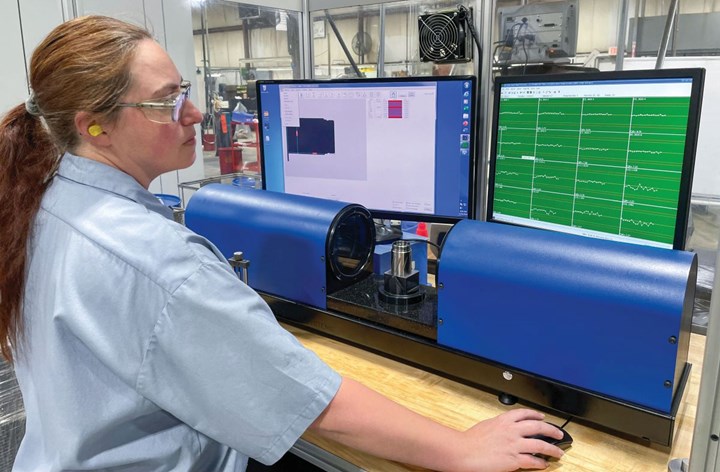
这样的自动视觉检测系统help alleviate measurement bottlenecks created when CNC multi-spindles significantly increase production volumes the shop must handle.
Per the former, the shop’s automated vision systems fromOasis Inspection Systemshave proven valuable in speeding part inspection. “We certainly don’t want to have to halt production on a CNC multi-spindle that might be dropping completed parts every 8 seconds to manually inspect them at specific intervals throughout a job,” Pouillie notes. “Fast, automated inspection processes enable us to satisfy quality reporting requirements while keeping these machines up and running.”
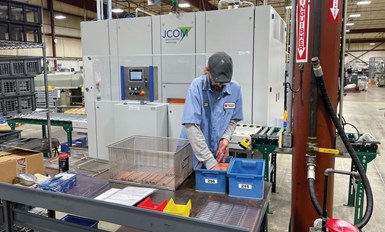
Like part inspection, part cleaning can become a bottleneck when production volumes increase. This is one reason why Mitotec Precision added a single-chamber, solvent parts washer with automated loading/unloading system.
Per the latter, Mitotec Precision added a single-chamber, vacuum-solvent parts washer with automated loading/unloading system fromJCOM Imports.清洗可以成为像检验部分,部分a bottleneck given the CNC multi-spindles are producing complex parts (sometimes having features such as blind holes) so fast. In addition, part cleanliness regulations continue to become more stringent.
Parts are cleaned by flooding the unit’s drum (with the option to swivel or tumble parts as well as use ultrasonics) to clean them to medical-grade standards (50 different cleaning programs/recipes are available). It is also operated under vacuum for energy efficiency and to help protect the machine components. Mitotec Precision is integrating a bar code system for each parts basket with the proper cleaning “recipe” to simplify the process for employees.
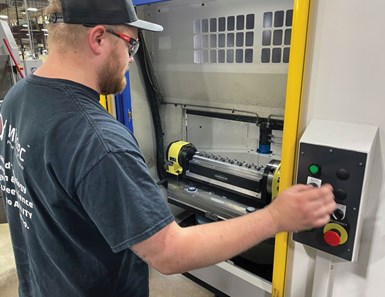
The CNC multi-spindles opened time on Mitotec Precision’s four VMCs that previously were used primarily for second-op work. Now, the shop is using machines such as this Brother VMC with pallet changer and hydraulic workholding for production work.
Conversely, the CNC multi-spindles have opened time on the shop’s four VMCs that previously were used primarily for secondary operations. Now, it uses these machines for production work. One example I saw during my visit was a small casting for a medical application run across a Brother VMC with pallet changer using hydraulic vises andPaws Workholdingsystem on a rotary table.
Read: The Right (Machine) Tool for the Right Job
Next Steps
The shop has taken further strides along the CNC multi-spindle path by altering the layout of its shop floor — not only to accommodate its second MultiSwiss, but additional CNC multi-spindles on either side of the current pair. One challenge for Sales Manager Warren Schoenborn, however, is finding new work to both generate a backlog on those machines while maintaining availability to work in a high-volume job when a customer needs it. Per the former, he’s eyeing new markets for the shop, such as medical and optics.
Regardless, this falls in line with Mitotec Precision’s mantra of thinking differently and creatively. This is an example of shops with which I enjoy staying in touch. Who knows what new process or technology a subsequent visit at some point might reveal.
RELATED CONTENT
How to Get More Efficient Production from Swiss-Type and Multitasking Machines
SolidCAM for multi-axis Swiss type and multitasking machines provides a very efficient CAM programming process, generating optimal and safe Mill-Turn programs, with dramatically improved milling tool life.
Reinventing The Multi-Spindle's Spindle Drive
Applying CNC to a multi-spindle machine must deal with the problem of independently powering each of the main spindles. A machine, new to the North American market, overcomes this problem with a unique approach.
Taking CNC Multis to a New Level
A visit to EMO, should be on the top of anyone’s list to see the latest in machining technology.